1 / CASE
The customer came to us looking for a manufacturer with in-house facilities to produce the complete product.
The case is developed in co-operation with the customer and their supplier of cover.
The customer wanted to simplify their supply chain and thereby be able to lower transportation and carbon footprint.
In this case, in-house manufacturing facilities for moulded foam and good upholstery engineering were the decisive factors.
2 / PROCESS
Together with the customer we decided to run the case as a double track.
Moulded foam has high start up costs in mould-tools. And moulds are not easily changed to do adjustments in shape or size.
Therefore shape, size and construction of the product was developed in cut foam. At the same time, we ran trials in moulded foam to explore textures and surfaces.
Once the prototype and moulded foam compound were approved, the next step was to complete the tooling and prepare for production.
3 / SOLUTION
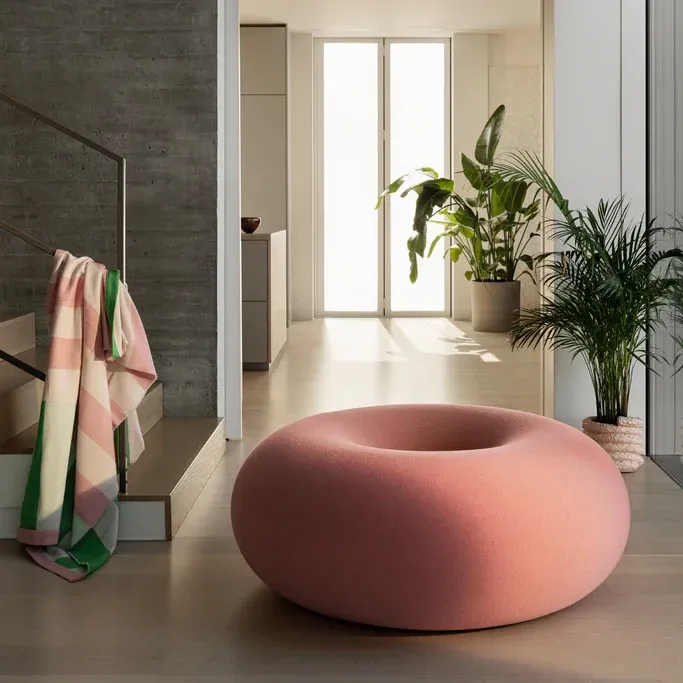
The final product was a round donut with a smooth surface and a nice sitting comfort.